Insights
How the manufacturing industry reduced risks by digitalizing
3 min read.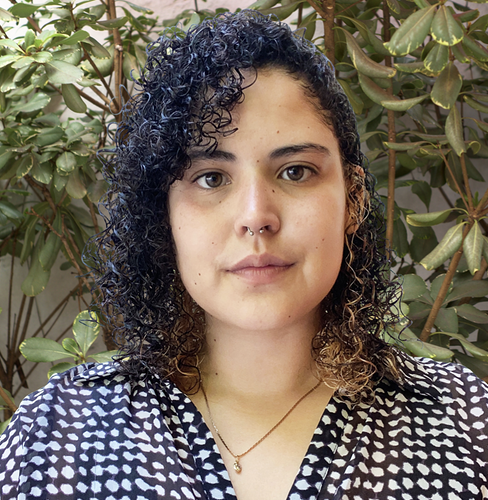
María Lucía Villegas
Strategy ConsultantThis year we complete two full years of the pandemic, with this, there have been multiple changes in the world how we know it. Naturally, the corporate world experienced the most changes as there was a shift in how we consumed and practiced our work life. As fast as restrictions started, the manufacturing industry was negatively affected by a lack of human resources to keep up with operations.
That is how the pandemic proved this industry is not only not prepared to face a sudden change or challenge but also it is extremely vulnerable without human labor. Take the 2008 financial crisis for example, it took manufacturers 3 years to recover or at least reach pre-crisis levels. How long is it gonna take to recover from covid?
But it’s fair to say that the manufacturing and logistics industries were not in the same place as the 2008 financial crisis. In 2020, many companies had started their digital transformation implementing different technologies to improve their operations. Those companies that were already one step ahead, technologically speaking, were the ones less affected by the sudden changes.
In a McKinsey survey companies whose industry 4.0 implementation is more mature report stronger ability to respond to crisis and 65% say their perception of industry 4.0 changed after the pandemic to more valuable.
However, the hype to digitalize was minimized as companies started seeing positive results. The same survey shows that while digital technologies were vital for companies in the beginning of the pandemic, now we’re seeing a drop in the ability to scale the implementation of these technologies. One of the reasons we see this drop may be because of an increase in expectations of what a successful digital transformation means.
It is evident we’ve become more demanding of our expectations in the digital world and as companies, are looking to be prepared for any crisis or disruption that we may face in the possible future. Not that the consequences of the pandemic are over though, we’re still, at this point seeing the negative backlash of this situation.
As we thought we were just about to get over COVID-19, there comes the variants. Countries like France and Japan are taking new measures to control the spread of the virus and with this, companies if not now, will be forced to keep changing their manufacturing dynamics to face problems like delivery delays and uncertainty. Add to this the economic crisis we got ourselves into and how inflation is reaching historic tops around the world, increasing costs.
So yeah, we’re just getting started on problems to solve. Gladly, where there is a problem, there is also a solution. There are different ways in how companies are using technology to improve day-to-day activities.
For example, one of them is the rise in the implementation of 3D printing. A CBInsights report shows companies are using this technology to accelerate product development, offer customized products and limited series, increase production flexibility and optimize demo products expenses. Now, 3D printing constitutes a $67B global market and, according to CBInsights’ industry analyst consensus it will continue to see increased adoption thanks to its value in rapid prototyping.
Another example is automation and robotics. We’ve mentioned this before in our top trends of 2022 lists because they offer a long-term solution for the manufacturing industry. Actually, automation and robotics were already on the rise prior to the pandemic. Today companies specializing in industrial automation and robotics saw an increase in demand, for Fetch Robotics, a company that provides autonomous mobile robots to warehouses, it increased 63% in just one month.
Like these, there are plenty of proves that digitalizing reduces risks in times of crisis. The first step is always identifying which technologies are better for your company, as every company is different. In the manufacturing industry, there is nothing but diversity since technology can cover every point of the production process. From mechanization to machine learning and AI, starting your digital transformation will only guarantee stabilization for your company.
But as we’ve said before, digitalizing is a process that takes years, needs to be executed throughout every area of the company, and implemented with a focus on the impact that it could have on the society and workers, like the new required skillsets of factory workers. For a successful digital transformation, the keyword is integration, from the integration of IT and OT to the integration of IoT and AI to big data and so on.
In conclusion, the manufacturing industry was one of the many industries that not only were negatively affected by the pandemic but also were forced to explore digital technologies to at least survive. But a global pandemic shouldn’t be necessary to start implementing new technologies as they are designed to increase productivity and add value to a company, the only thing you need to do, is identifying which ones are best for your business.
Written by María Lucía Villegas
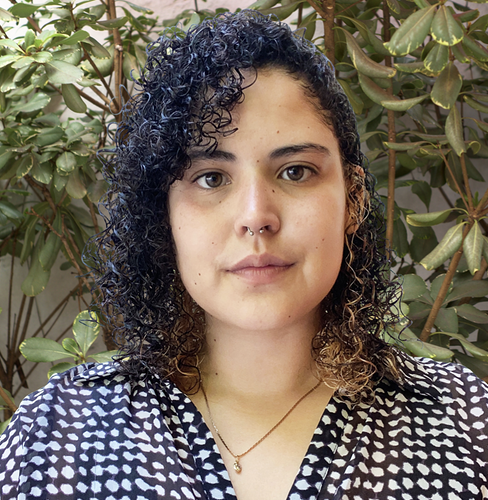
Lu provides expert guidance in shaping business strategies and achieving growth. Her analytical skills and industry insights help clients navigate challenges and capitalize on opportunities.